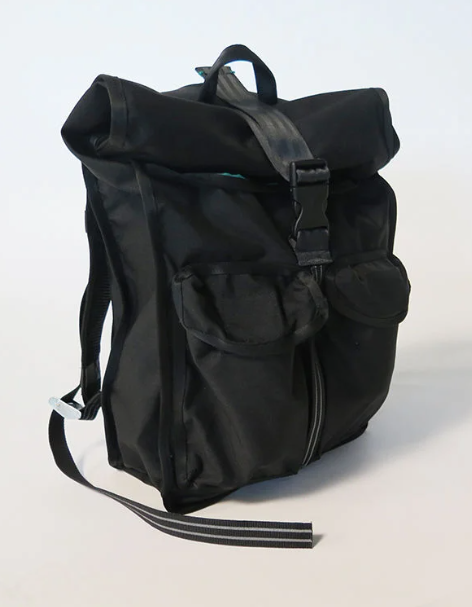
A Complete Guide to Making a Backpack: From Concept to Creation
Backpacks are essential items that we use daily to carry everything from school supplies to hiking gear. But have you ever wondered how these bags are made? What goes into crafting a backpack that’s functional, stylish, and durable? In this guide, we’ll explore the process of creating a backpack, from material selection to final production, giving you an in-depth look at the steps involved in making a great backpack.
What Materials Are Used to Make a Backpack?
The material used in a backpack is the foundation of its design and functionality. Whether it’s a lightweight fabric or a durable leather, each material serves a specific purpose. Let’s look at some of the most common materials used in backpack manufacturing:
- Polyester: Lightweight and affordable, polyester is commonly used for everyday backpacks due to its durability and water resistance.
- Nylon: Known for its strength and tear resistance, nylon is used in outdoor and performance backpacks where durability is key.
- Canvas: Heavier than synthetic fabrics, canvas offers a rugged look and is popular for eco-friendly and casual backpacks.
- Leather: A luxurious option, leather is often used in high-end backpacks. It’s durable and ages well, developing a unique patina over time.
- Vegan Leather: An environmentally friendly alternative to traditional leather, offering a cruelty-free and low-maintenance option.
Each material has its pros and cons, and the choice of material depends on the intended use of the backpack. For example, nylon is ideal for outdoor activities due to its resistance to abrasions, while leather suits fashion-conscious individuals looking for something durable and stylish.
How Do Different Materials Impact Durability and Functionality?
- Polyester vs. Nylon: While polyester is lightweight and cost-effective, nylon offers superior tear resistance, making it more suitable for outdoor and performance backpacks.
- Canvas vs. Leather: Canvas provides durability at an affordable price but lacks the luxurious feel of leather, which offers longevity and a refined aesthetic, especially for business and fashion backpacks.
Eco-friendly alternatives, such as recycled polyester and organic cotton, are increasingly popular for environmentally-conscious consumers who still want high-quality products.
How Are Backpack Designs Created?
The design process is just as important as the materials used. A well-designed backpack doesn’t just look good—it’s built to function efficiently. Key elements of backpack design include:
- Compartments and Pockets: The number and layout of pockets influence the organization and accessibility of the bag. Larger backpacks, such as those for travel, often have multiple compartments, while smaller ones may focus on easy access to essentials.
- Straps: Shoulder straps, along with back padding, are essential for comfort, especially when carrying heavier loads. Ergonomic straps help evenly distribute weight, reducing strain on the shoulders and back.
- Closure Systems: Zippers, Velcro, and drawstrings secure the backpack contents. Zippers offer more security, while drawstrings provide easy access, especially in bucket-style bags.
Designers typically choose features based on the intended use of the backpack. For instance, a travel backpack may have hidden security pockets, while a school bag might prioritize compartments for books and laptops.
Tools and Equipment Used in Backpack Manufacturing
Creating a backpack requires more than just the right materials and designs—it also involves the use of various tools in the production process. Here’s a look at some essential equipment used to craft backpacks:
- Cutting Machines: These machines precisely cut fabric, leather, and other materials to the desired shape.
- Sewing Machines: Industrial machines are used to stitch the fabric pieces together, forming the structure of the backpack.
- Rivets and Fasteners: Used to attach hardware like buckles and straps, ensuring the backpack is durable and functional.
- Laser Machines: Ideal for precise cutting, especially with synthetic materials, reducing waste and improving efficiency.
Industrial machines enable manufacturers to produce high-quality backpacks at a faster rate while ensuring consistency. Automated tools, including laser cutters and sewing machines, speed up the process and reduce costs.
How Are Backpacks Assembled?
After materials are chosen and designs are finalized, the assembly process begins. Here’s how backpacks are created step by step:
- Cutting: The fabric is cut into the necessary panels using rotary or laser cutting techniques. Laser cutting is often preferred for synthetic materials because it offers cleaner edges, reducing the risk of fraying.
- Sewing: The panels are stitched together using strong industrial sewing machines. Reinforced stitching is used in areas that will bear the most weight, such as the straps and zippers.
- Adding Hardware: Buckles, straps, and zippers are attached using rivets and fasteners to complete the backpack’s structure.
Each piece is carefully stitched together to ensure that the backpack is both durable and functional. Reinforcement stitches are typically added in areas that experience the most stress, like strap attachments.
Quality Control in Backpack Manufacturing
Quality control is a critical part of the backpack production process. Manufacturers conduct rigorous inspections to ensure the final product meets safety and durability standards. Here’s how quality control plays a role:
- Prototyping: Creating prototypes helps visualize the design and functionality of a backpack before full production begins. This ensures the product meets both design and practical requirements.
- Durability Testing: Backpacks are tested for strength, water resistance, and wear and tear to make sure they perform well under everyday use.
- Consistency: Manufacturers ensure that all backpacks are produced to the same standard by conducting checks at various stages of production.
Quality control ensures that the backpack will withstand regular use and maintain its structure over time. Tests are done to check fabric durability, zipper function, and overall wearability.
Customizing Backpacks for Branding and Special Features
Customization adds a personal touch to backpacks, allowing brands to add logos, designs, and special features. Here’s how customization works:
- Logo and Print Options: Embroidery and screen printing are the most common methods used to add logos and graphics. Embroidery offers a premium, textured look, while screen printing is ideal for bold, colorful designs.
- Special Features: Brands can add custom features such as additional pockets, RFID-blocking compartments, or ergonomic straps to improve functionality.
- Material Customization: Customers can also choose specific fabrics, colors, and textures to create a personalized backpack.
Customization options vary based on the desired look and functionality, giving companies the ability to design backpacks that reflect their identity and meet customer needs.
How to Test a Backpack’s Durability
Before being released to consumers, backpacks undergo several durability tests to ensure they can withstand daily wear. Some common tests include:
- Zipper Tests: Zippers are tested to ensure they can handle frequent use without failing.
- Fabric Durability: Abrasion tests assess how well the fabric holds up against repeated friction, and water resistance tests check how the material performs in wet conditions.
- Weight Testing: Backpacks are tested to ensure the straps and seams can carry the weight of typical contents without breaking.
These tests help ensure that the final product is durable and can stand up to the challenges it will face during use.
Conclusion
Making a backpack is a complex process that involves choosing the right materials, designing for functionality and comfort, and using specialized equipment to assemble the product. With careful planning and attention to detail, manufacturers create backpacks that are not only durable and functional but also stylish and customizable. Whether you’re designing your own or purchasing one, understanding how backpacks are made gives you a deeper appreciation for the craftsmanship behind these everyday essentials.